AutoForm: Simulate shaping operations Planned operations by default improve deep drawing
Author / Editor: Theo Drechsel / Konrad Mücke
The Virtual Production Institute at ETH Zurich in collaboration with Autoform developed a method to automatically organize the molding processes. With this, Franke Kitchen Systems lowered the reject rate at deep draw sinks.
Companies on this topic
(Image: Autoform)
Deep drawing of sheet metal is one of the classics in shaping processes. In this process, the metal sheet is drawn into the die using the drawing hole, creating the desired shape. One or more fastening devices ensure that no wrinkles form in the edge area. “In practice, it starts with cold tools that are heated up at startup. In order to be able to produce sheet metal parts at this condensation stage, the clamping forces must be constantly corrected,” explains Dr. David Harsch, who dealt extensively with these issues while receiving his Ph.D. at the Institute for Virtual Production (IVP) at ETH Zurich. The heating of the tools due to friction will not be bad on its own. However, the conditions of friction also change with temperature. Knowledge and experience of journalism is required here. But even the most experienced employee often cannot prevent rejection from occurring, depending on the particular pelvic model. In the case of kitchen sinks with a larger sink radius of 36 mm or more, there is no average glow, which greatly increases the risk of rejection.
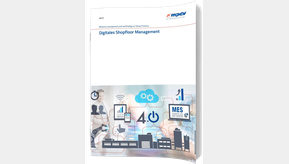
With a chain as small as five percent of scrap
“The rejection rate here is five percent for small batches,” confirms David Harsh. Since receiving his PhD in IVP in close collaboration with Autoform and Franke, he has been working for Franke as a development engineer and project engineer. One of his areas of responsibility there is to improve the production of kitchen sinks. The business owner is a subsidiary of the Franke Group, which operates in 40 countries and is headquartered in Aarburg, about 60 km west of Zurich.
Franke’s Kitchen Systems division produces around 300,000 basins annually in Switzerland alone, and with nearly 5 million basins, it is one of the largest suppliers in this field worldwide. Franke’s product range currently includes over 1100 different models of sinks worldwide. “The quantities to be produced are only between 25 and 200 pieces.”
David Harsch emphasizes, referring to his PhD project called Q-Guard, initiated by ETH Zurich and in close cooperation with the software manufacturer, “Due to the sometimes small batch sizes, it is especially important to produce the fewest rejections possible” Autoform was achieved. In Franke.
Based on simulation models
“We have dealt with the issue of process observation in deep drawing for many years at the institute,” says Dr. Jörg Heingärtner, who holds a PhD in Engineering from IVP from ETH Zurich, researches new production processes. The procedure used in parts of the Q-Guard project is known. It is the measurement of sheet metal pull and comparison with a reference part in order to use the values obtained in this way to change the compressive forces in a manner that ensures quality in the chain. “We also judge quality based on the paper feed. Jörg Heingärtner explains the idea we took at Q-Guard even further.” Our approach is to completely design this controller based on the simulation results of the deeply drawn portion. We wanted to have Autoform on board because they are the competent partner for this and with the Autoform-Sigma product they have had a very powerful tool for improving sheet metal forming processes for many years. ”
Method diagram generates control parameters
As Autoform’s Product Manager, Andreas Krainer accompanied this project extensively. “The Autoform-Sigma based control algorithm calculates how to modify and distribute compressive forces in order to return sheet metal feed to their target value,” says Andreas Krainer, explaining the role Autoform-Sigma plays in controlling the embedded process. In the preceding period, an analysis is carried out with Autoform-Sigma, in which compressive forces and material parameters are varied. Andreas Krainer says: “It could work as follows: The style diagram designs the tool, then runs Autoform-Sigma through it and presents the control parameters on the USB stick that are taken into account at the start of production.” “The result of the analysis is a model in which the relationship between indentation and manipulated variables is modeled. A perfect match between reality and simulation is not necessary as long as trends are represented correctly.” Another result of the simulation is to determine the positions where the indentation is to be measured. IVP’s Jörg Heingärtner adds: “Basically, indentation can be measured visually or by touch.” The Q-Guard project in Arburg decided on a single camera recording the outlines from above with blue light: “Because we do not measure indentation of the entire sheet metal portion, but only at pre-computed points using Autoform-Sigma.” Another important point is the issue of tribology and hence friction. Since Franke stated that temperature sensors would not be integrated into the instrument for review reasons, appropriate tests were performed to assign a realistic coefficient of friction in the simulation model.
Material properties are taken into account
In addition, changing materials’ properties had a strong effect on the result of deep drawing, according to David Harsh: “Frank treats materials from different manufacturers, some of which have completely different properties.” That is why an eddy current meter and laser measuring system were installed on the cutting machine in Arburg. The first is used to determine the material properties of each blank piece, and the sheet thickness is recorded by laser. The data obtained is passed to the feeding control. In contrast to fluctuations in process parameters, the material dispersion is corrected here without a forward feed control loop based on descriptive models and transferred to the PLC for pressure. After deep drawing, the measured drag is compared with the nominal drag by the camera and the difference is transferred to the control unit as a control deflection (feedback loop). From this, the control algorithm calculates the new compressive strength of the next segment and, accordingly, the forces of the four compressors present in this tool.
Reports data matrix individually
So this is the control loop. For this purpose, Autoform has implemented an interface so that Autoform sigma data can be used accordingly. David Harsch adds: “Based on the results of Autoform Sigma, we designed and implemented the feedback loop control module and were also able to develop the descriptive models used in feeding control.”
After cutting, eddy current measurement and sheet metal thickness recording, blanks are printed with data matrix code and stacked for identification. In front of the press, the robot then individually places the blanks on a conveyor belt, the code is scanned and the mechanical properties of the respective blanks are recalled from the database. On the basis of this data, advance control of the press is carried out. Then the vacuum is reshaped in the hydraulic press (Schuler, clamping force 8000 kN), the sump is removed by a robot using a device, which is placed under the camera and measured. “It’s important to be as close to reality as possible when comparing the actual objective / situation,” says David Harsch. “This is why we are always digitizing a large portion of the current production and comparing it to the simulation model.” Is everything working as planned now? Jörg Hingartner replies, “Basically yes.” Of course, with the process control involved, there are also parts that are rarely rejected. “Including all the outliers, one would say we have reduced the rejection rate by two thirds.” In addition, the system can handle very thin laminates and tolerate faults. “As part of the test, we intentionally distorted the press completely. Here too, the console found its way into the good parts in a very short time. ”
Control operations are included
There are plans to implement more process controls included in other Franke plants. Additionally, IVP is working with another project partner – a German automaker – as part of Q-Guard. David Harsch is also very satisfied with the result of the Q-Guard project. In this context, he touches on another point very important to Frank – the experience of those working in the press: “The staff knows exactly how the tub should be produced with any force. If these people fail, it might be a good thing that some models of billiards can no longer be produced as they are today. “. This is because you move in a very narrow window between notches and ripples when making the tub, which can quickly lead to rejections and machine downtime when the tool is heated up. “With process control, the drawing result always remains good in the process window and the rejection rate tends towards zero.” SMM – SMM
(ID: 47374382)